Have you ever been curious about how surfboards are made? Whether you are a seasoned surfer or just starting out with surfing, having a well-made surfboard is a key ingredient to having a good surf session.
Here at Bodhi Surf and Yoga, we offer many high-quality boards for use during surf lessons. Creating these high-quality surfboards is a combination of art and science, where different surfboard shapers bring their own style and vision into creating the perfect surfboards for all kinds of wave riding.
The process of making a surfboard, from idea to a finished project, is detailed and complex. Genaro Garro, a local surfboard shaper and designer in Uvita, Costa Rica, describes the process of making a surfboard as creating art.
“Every step through the surfboard manufacturing, it’s an art on its own. I shape, I design. That’s an art, right? You get a big block of foam like a painter gets a canvas, and you make it into something beautiful. Like an artist trying to design something out of stone, and hammering away. That’s what I’m doing; I’m just hammering away.”
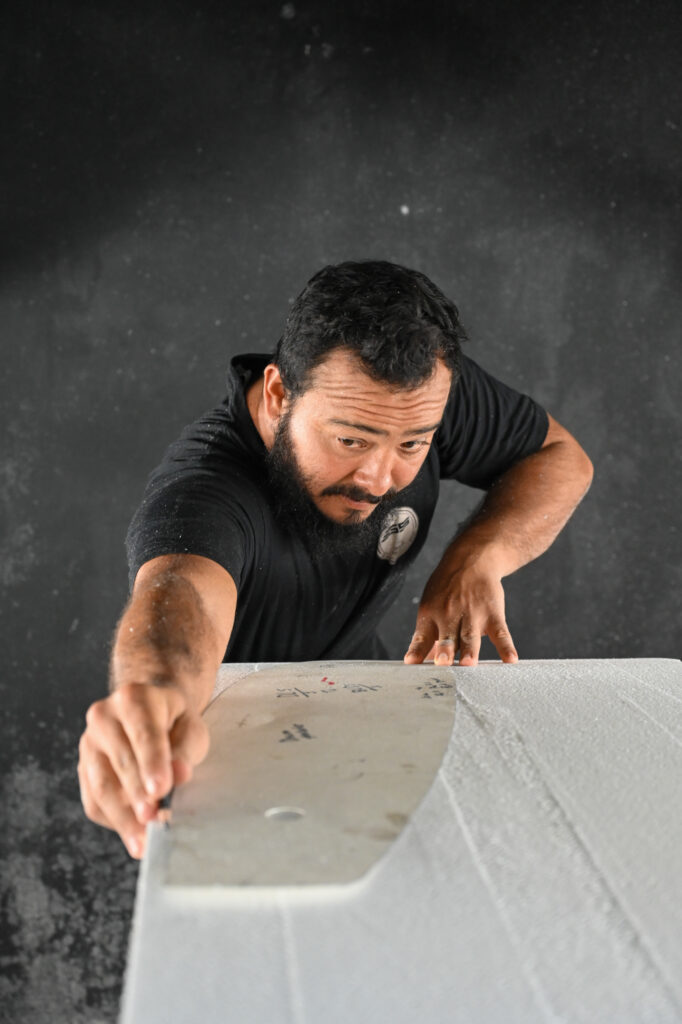
for what specific type of surfboard is being made.
The Parts of a Surfboard
Before explaining how surfboards are made, it is important to briefly explain the parts of the surfboard to understand how a surfboard works and how these parts affect its performance.
A diagram of a surfboard will show you all the different parts, from top to bottom. Here’s a quick breakdown of it all:
1. Deck
The deck is the top surface of the surfboard where the surfer stands. It’s usually covered with a traction pad or wax to provide grip and prevent slipping.
2. Bottom
The bottom is the underside of the surfboard that makes contact with the water. It plays a critical role in determining the board’s speed, stability, and maneuverability from the flow of water underneath.
3. Rails
Rails are the edges of the surfboard running from nose to tail. They influence the board’s turning ability and responsiveness. Soft rails provide a smoother ride, while hard rails offer sharper, more precise turns.
4. Nose
The nose is the front part of the surfboard. Its shape and design impact the board’s paddling efficiency and ability to handle different wave conditions. A pointed nose is typical for shortboards, while a rounded nose is common in longboards.
5. Tail
The tail is the back end of the surfboard and comes in various shapes. Each tail shape (round, square, squash, etc) affects the board’s control, speed, and maneuverability.
6. Fins
Fins are attached to the bottom end of the surfboard and are very important for steering and stability, and the setup of fins can drastically change the way a surfboard performs. Common setups include single fin, twin fin, thruster (three fins), and quad (four fins).
7. Leash Plug
The leash plug is a small, reinforced hole where the leash is attached. The leash is a cord that connects the surfer’s ankle to the surfboard, ensuring the board remains close to the surfer after a wipeout.
8. Stringer
The stringer is a thin strip of wood running down the center of the surfboard from nose to tail, providing structural integrity and stiffness.
9. Laminate
The laminate layer consists of fiberglass cloth and resin, which is applied to the foam core of the surfboard. This layer provides strength and rigidity while protecting the board from water damage.
10. Foam Core
The foam core, or blank, is the foundation of the surfboard, giving it shape and buoyancy. It is typically made from polyurethane (PU) or expanded polystyrene (EPS) foam.
Surfboards also come in many different sizes, from longboards to mid-lengths, to shortboards.
Shortboards are typically under 7 feet long and designed for quick turns in more powerful waves. Mid lengths, ranging from 7 to 8 feet, offer a balance between the maneuverability of shortboards and the stability of longboards. Longboards, usually over 8 feet, provide excellent paddling ease and stability, perfect for smooth, graceful riding on smaller, gentler waves.
You can find a lot more details about this if you check out our Bodhi Surf and Yoga Blog about the different types of surfboards.
When it comes to the difference between his approach to making longboards versus shortboards, Genaro compares it to how someone dances to different types of music.
“If I bring some of my friends who are longboarders or twin fins or mid-lengths people, they’re going to ride a longboard as it should be ridden… with flow, style, and delicate, very delicate. If you are a dancer, you dance bachata, or you dance differently to a wedding waltz. I want to make a board that is very specific to the style that my client wants to ride.”
Materials Used in Making Surfboards
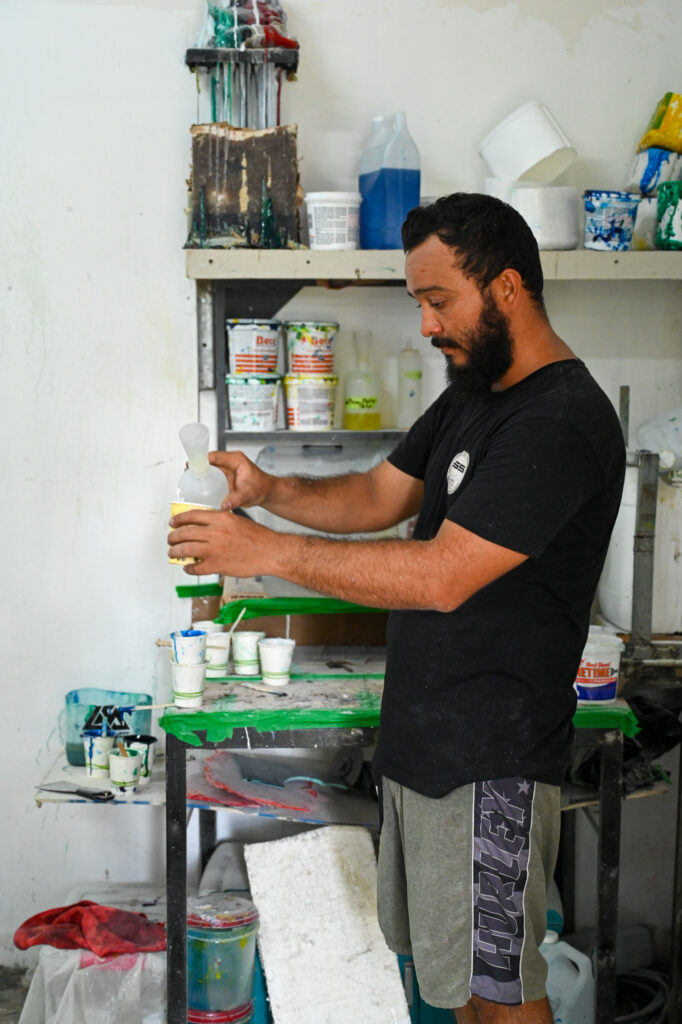
perfect for catching waves and enhancing your surfing experience.
The core of the surfboard is always going to be epoxy or polyester. Although surfboards can be made out of wood (though it is rare these days), there is always foam inside the core.
Surfboards are primarily made from foam, fiberglass, and resin. The foam core, often polyurethane (PU) or expanded polystyrene (EPS), provides the board’s shape and buoyancy.
The way the fiberglass comes out is going to make a huge difference to the durability or flexibility of the board.
Fiberglass cloth is layered over the foam, adding strength and flexibility. Resin, either polyester for PU foam or epoxy for EPS foam, is applied to harden the fiberglass and create a durable, water-resistant outer shell. Some boards may also incorporate carbon fiber for added strength and performance.
There’s a lot of hot debate in the surfing world about the pros and cons of epoxy surfboards, but in the surfboard-making process, it all comes down to the preference of the client and what they are looking for their surfboard to do in the water.
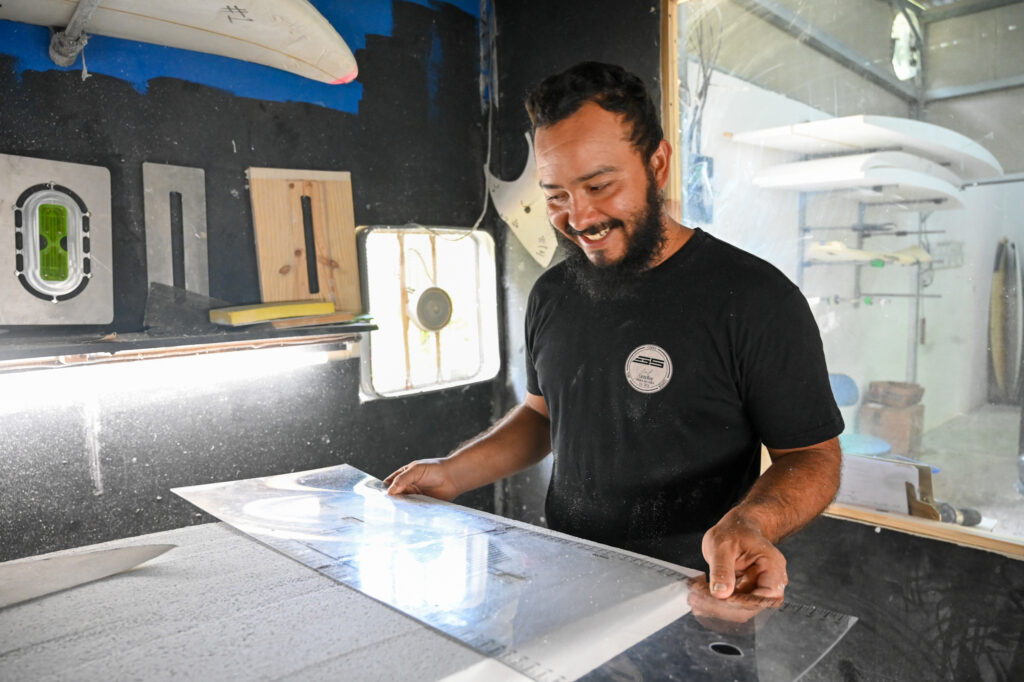
expanded polystyrene (EPS) foam.
Shaping the Surfboard
Surfboard shaping is an initial stage of surfboard construction. Before shaping a board, Genaro says that the most important thing for a surfboard shaper to do before starting a custom board is to thoroughly understand the specific needs and preferences of the surfer. This includes their skill level, surfing style, and the types of waves they will be riding.
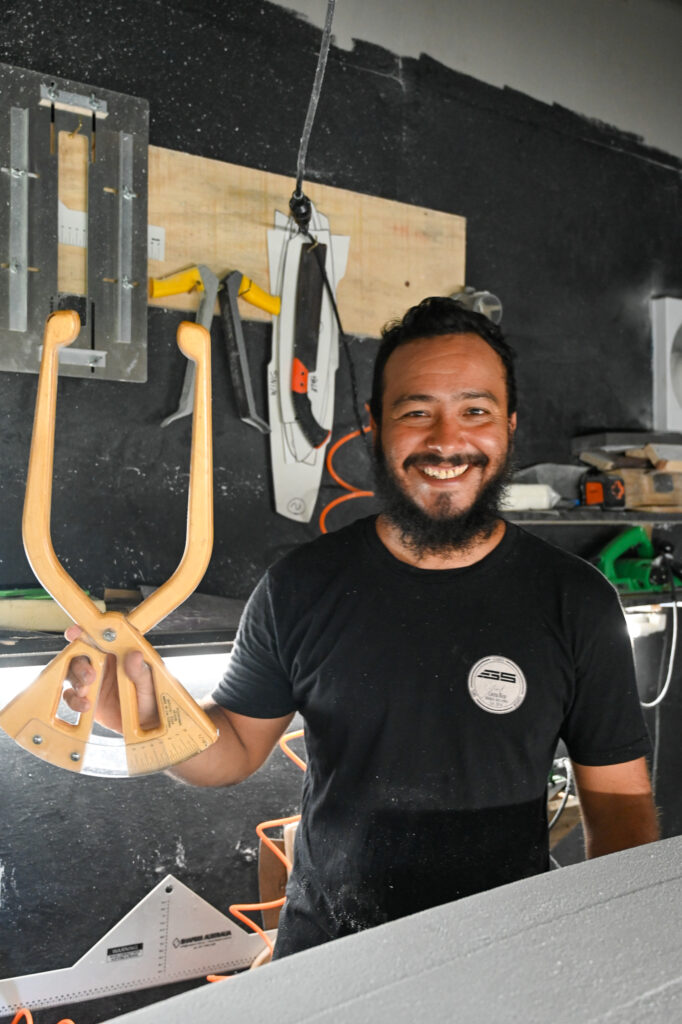
“The most important part to know before I design a board is the expectations of the person who wants the board. When you design a surfboard, every board is going to have to sacrifice something. You can’t have it all in one surfboard.”
The process of shaping a surfboard begins with a foam blank that is cut and sanded to the desired shape.
Next, fiberglass cloth is layered over the shaped foam. Resin is applied to harden the fiberglass, which creates a strong, smooth outer shell. Finally, fins, a leash plug, and any additional design features are added to the shape.
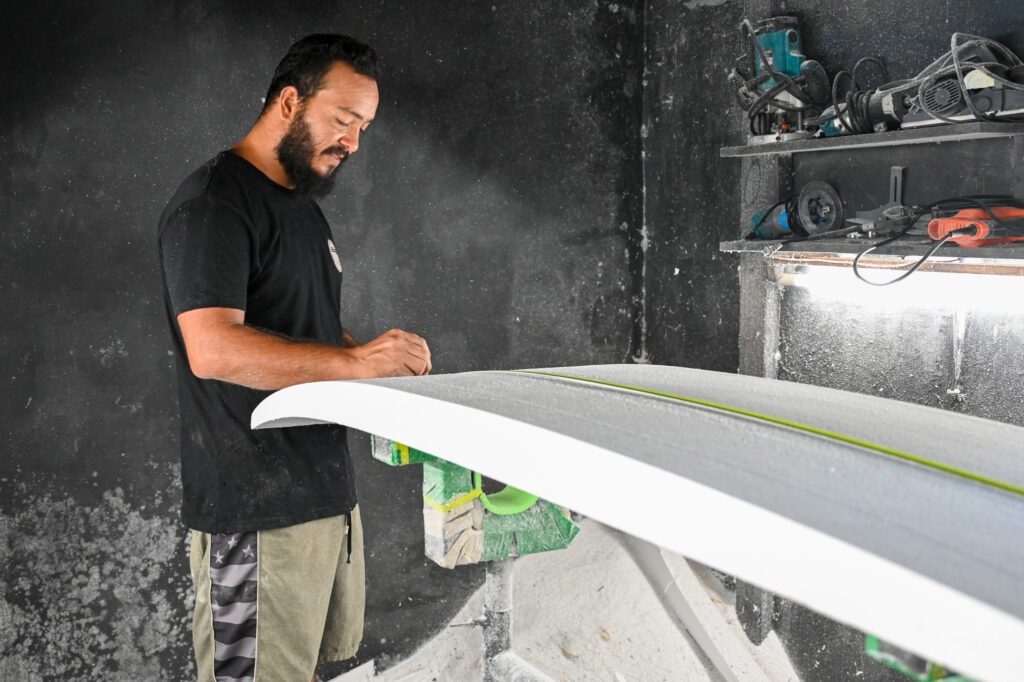
Surfboards can either be shaped by hand or by machines. Hand shaping allows for a personalized touch, offering custom designs tailored to a surfer’s specific needs and preferences.
Machine shaping provides precision and consistency, producing high-quality boards with exact specifications. It’s more commonly found in big name surfboard brands with mass production of boards.
The choice of whether to shape by hand or with machines is entirely dependent upon the shaper’s own unique approach to making surfboards.
“I shape everything by hand,” says Genaro. “I don’t like making copies of other people’s designs.”
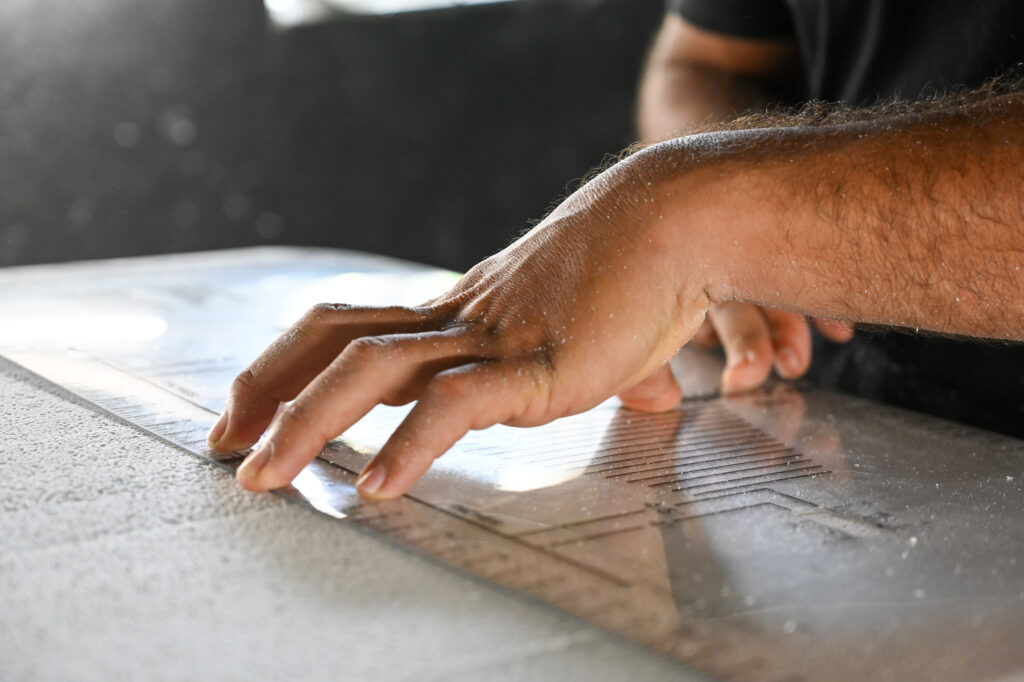
The rails of the surfboard are one of the most important and final steps in the surfboard shaping process.
Genaro says that “… after taking all the dimensions and thickness, I will move on to the rails. You want to take your time shaping the rails. You can make the exact same board, but if you change the rails, it’s going to feel completely different when you ride it.”
Glassing and Laminating
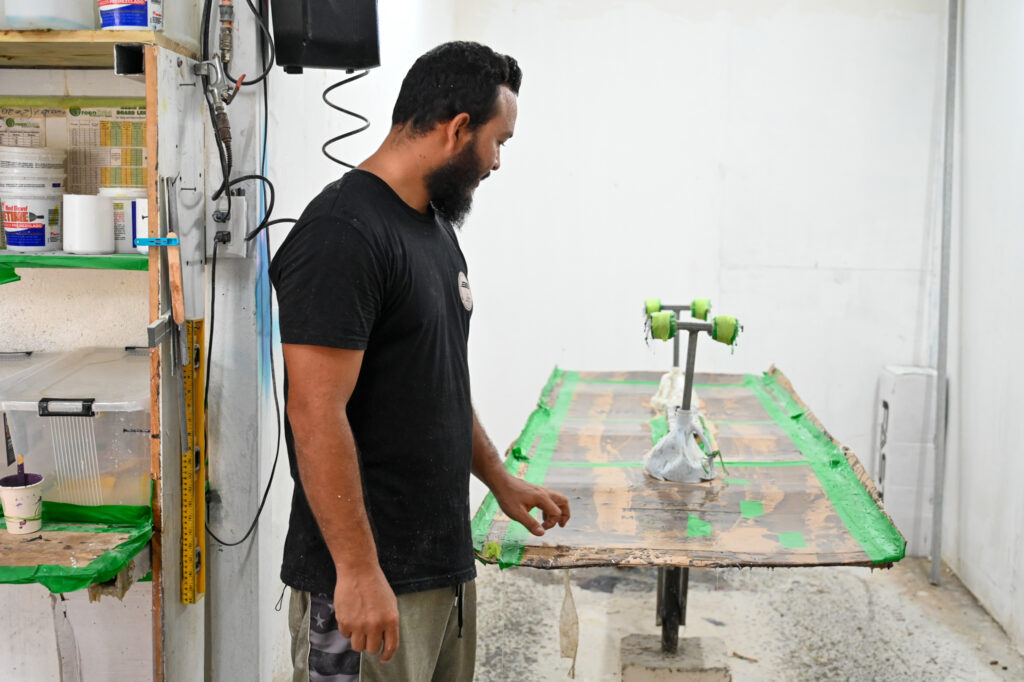
The next step after shaping your board is glassing and laminating. Glassing happens when fiberglass is put on the surfboard to help it stay durable during surfing. Laminating happens when you place an extra coat of fiberglass on the surfboard. Then it hardens, creating a tough, water-resistant outer shell.
During the glassing stage of surfboard making, the resin typically takes about 2 to 4 hours to harden, depending on the type of resin and also the environmental conditions like temperature and humidity. Epoxy resin generally takes longer to harden compared to polyester resin.
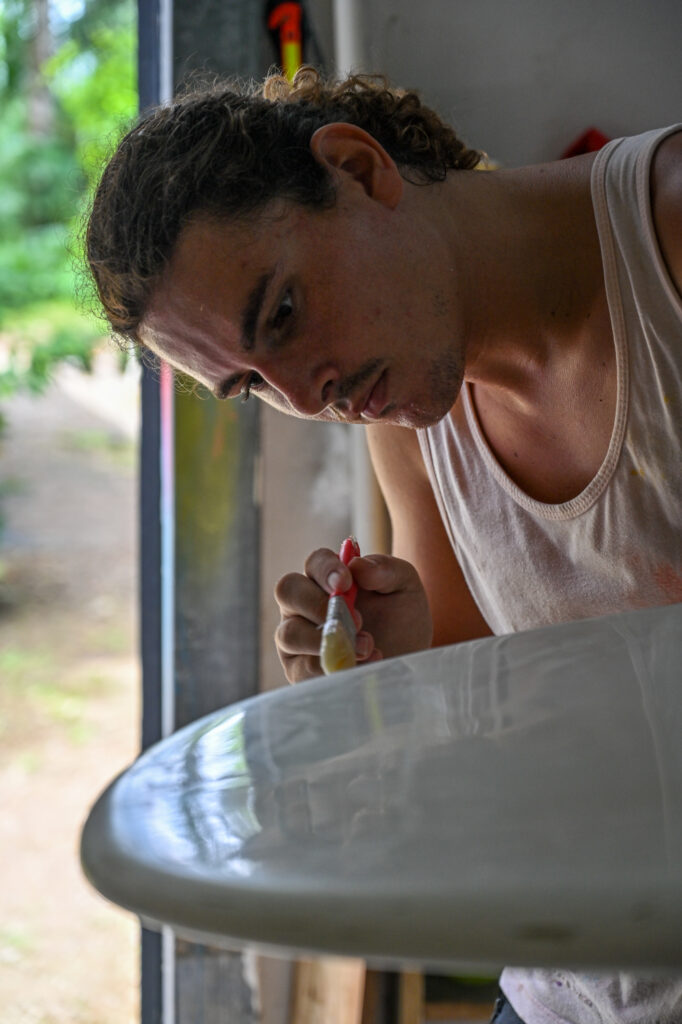
repair an EPS core surfboard.
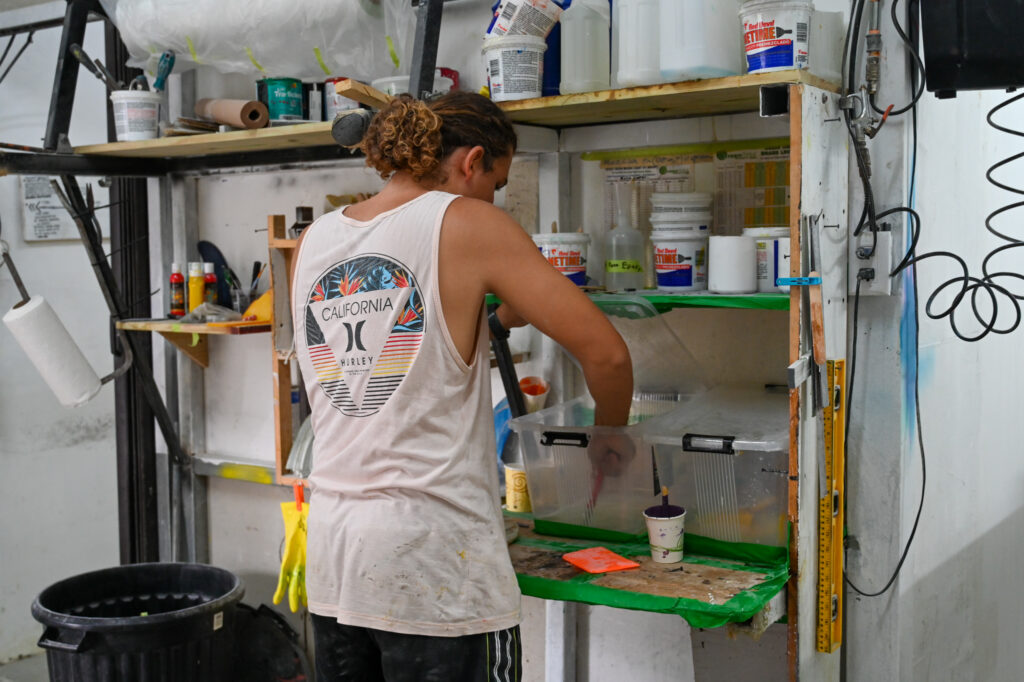
must be very careful not to cross-contaminate the two.
Aside from being something very cool to watch, Genaro says that glassing and laminating are often a very overlooked step in the surfboard-making process.
“That’s one of my personal theories about why surfboards break, because of not being delicate about the way you put fiberglass on the boards during these steps.”
During the process of making surfboards, it’s crucial not to mix polyester resin with epoxy resin, especially when laminating or glassing a surfboard. Polyester resin and epoxy resin are highly incompatible chemicals that can cause the fiberglass layer to peel, and can affect the structural integrity of the board.
Sanding and Finishing
The stage of sanding and shaping a surfboard is where the surfboard really starts to come to life.
Shaping begins with cutting and smoothing the foam blank to the desired design. After glassing, the board undergoes sanding to smooth out the hardened resin, which also removes imperfections.
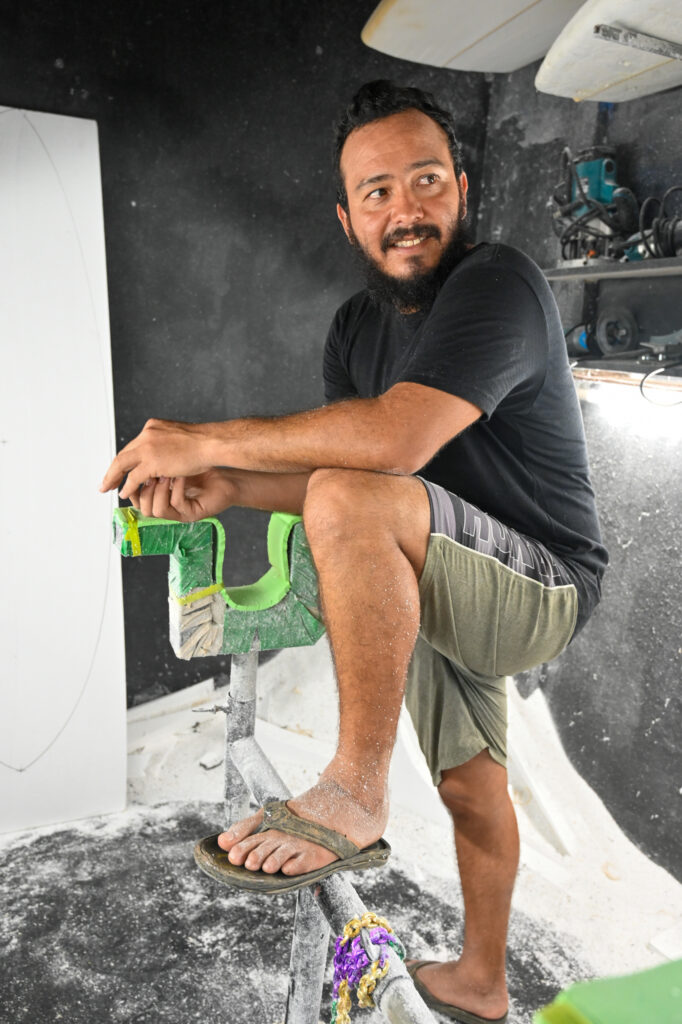
Genaro says that sanders and finishers are too underestimated in the surfboard-making process.
“As good as shapers are, the sanders are the last process of a surfboard. The entire process is important, but the sander and the glasser are the ones who really give life to the foam. The minute the labels, the fiberglass, the tint, the colors are applied, the board takes form and suddenly goes from being a bunch of materials to becoming its own special thing.”
Sanding also involves a lot of communication between client and shaper.
“Too much resin on the edges, and it’s going to change how it’s going to ride. A sander also has to know the expectations of the shaper and the client to really finalize that product and give the client the board they want,” says Genaro.
Fins and Final Touches
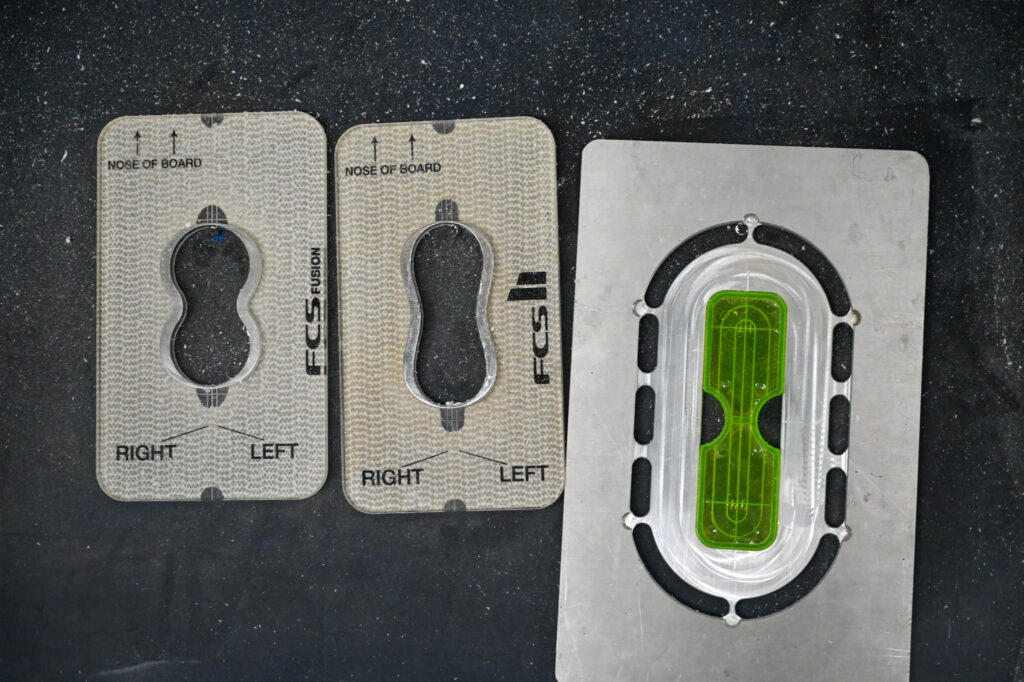
Surfboard fins help provide stability and lift and come in different configurations that affect the physics of how a surfboard moves in the water.
After shaping and sanding the foam blank, precise measurements are taken to mark the fin placement. Proper installation ensures a surfboard’s best performance.
Using a specialized router, slots are cut into the board where the fin boxes will be installed. These slots must be accurate to fit the fin boxes securely; otherwise, the fins will not fit with the surfboard.
Before a surfboard is handed off to a client, it must go through quality control, where the surfboard is inspected for anything that might have gone wrong through any of the previous steps.
Artwork, color, and prints added to the previous steps of the surfboard-making process are another of the special touches that make a surfboard unique.
Genaro does take custom surfboard art requests, and enjoys adding colors and patterns to boards. But he prefers to focus more on how a board performs versus how a board looks.
Even though specific colors are often requested by clients, Genaro says that it’s merely a customization in the process. “Personally, I don’t care how aesthetically a board looks. If it can ride and perform well, that’s what I really want.”
The Future of Making Surfboards
Surfboard styles, like fashion, tend to get recycled over the decades. For example, right now, 1960s retro-style longboards are becoming increasingly popular. Surfboard shapers do have to pay attention to trends and designs throughout history in order to sustain their business and give clients the surfboards they want to use.
With the rise in surfing’s popularity also comes the rise of more and more shapers to the industry. Genaro says it’s important to put aside ego in the industry, and it is most important to focus on improving the environmental impacts of making surfboards.
“I don’t care who comes into the surfing industry, as long as the changes are more conservative, in the sense of, can we create projects to recycle our stuff? Like foam. We produce a lot of foam, and a lot of this foam goes to waste.”
Genaro would love for everyone to be more conscious about buying recycled foam in the future.
“So, I personally am going to try and make tackling that a priority. I don’t care if I have to pay somebody a lot of money for someone to come and pick up my foam and take it to do whatever they can do with it. But, I want to make sure that whatever they do with it, make sure it’s being reused so that we can cut down on waste.”
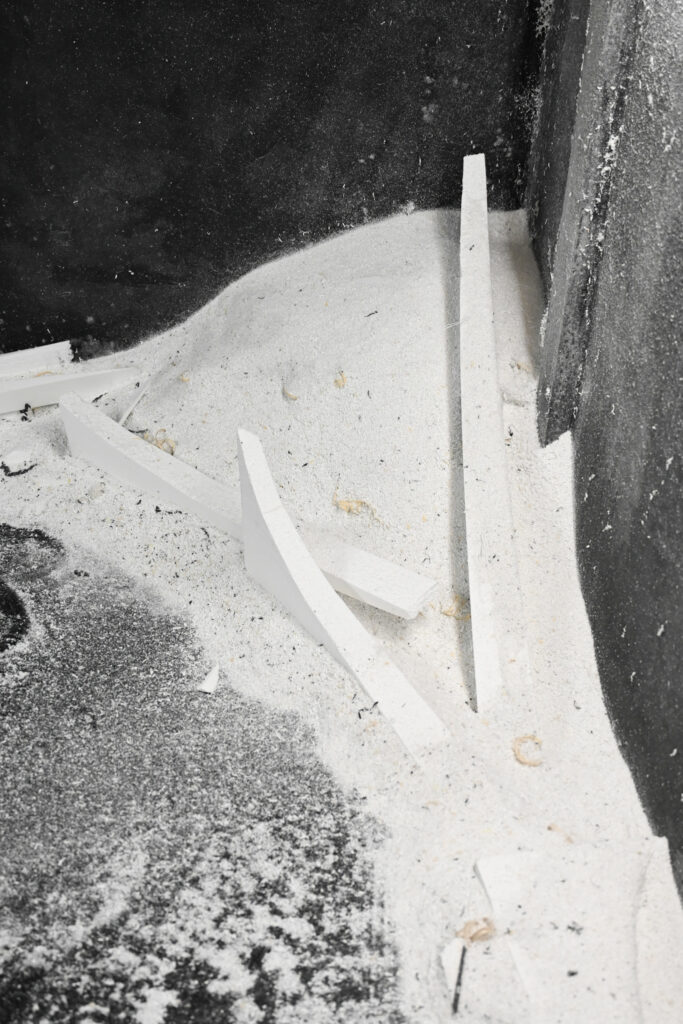
“I say, let’s try to make a change, you know? So, that’s where I would like the surfing industry to go. To have new people come in who are open-minded and environmentally conscious.”
In this world where so many items are mass-produced, made for only single use, and rarely carefully crafted by hand, it’s refreshing that this trade exists. Each board, meticulously shaped, glassed, and finished, is made by people who care deeply about the sport of surfing and their craft.
Embracing this artistry allows every wave rider to connect with their board on a deeper level, appreciating its unique blend of aesthetics and performance.
So, whether you’re a shortboarder, longboarder, a beginner, or an advanced surfer, let’s celebrate the beauty of surfing and the boards that we surf, as an art form made possible by surfers, for surfers.
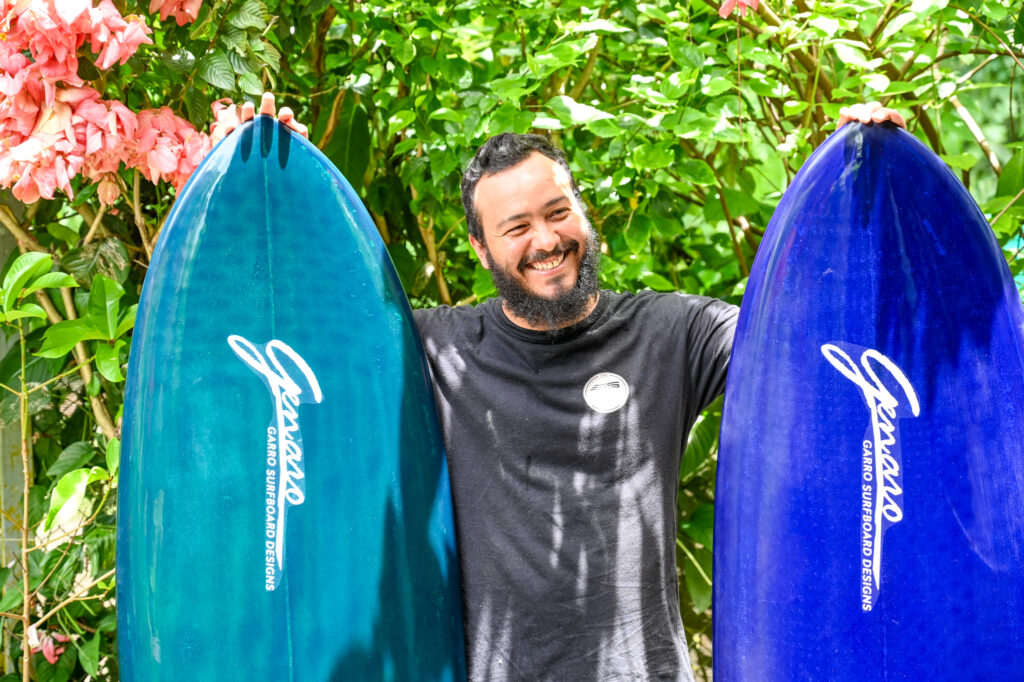
Get Step-by-Step Surf Lessons in Your Inbox
Learn to Catch Waves with our free 5-day email series from one of our lead surf instructors here at Bodhi Surf + Yoga.
Change the heading on the Separator tab ->
Search
Get Step-by-Step Surf Lessons in Your Inbox
Learn to Catch Waves with our free 5-day email series from one of our lead surf instructors here at Bodhi Surf + Yoga.
Change the heading on the Separator tab ->
Most Read Blogs
What is the Meaning of Anjali Mudra?
May 27, 2020
Fitness for Surfers: Workouts, Exercises & Training
February 10, 2022
The Best Places to Eat in Uvita, Costa Rica
May 19, 2022
How to Get From SJO to Costa Ballena, Costa Rica
May 31, 2018
Change the heading on the Separator tab ->
Categories
Categories
- Bodysurfing (5)
- Food (6)
- Responsible Business (6)
- Surfing (59)
- Travel (62)
- Yoga (38)
Change the heading on the Separator tab ->
Newsletter
Thanks for subscribing! Please check your email for further instructions.
Change the heading on the Separator tab ->
Follow Us
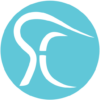
Allison Mouret
Change the heading on the Separator tab ->
Read more
A Typical Day: Bodhi Family Surf Camp
Words by George Frost
If you’re looking for a truly special bonding and connecting experience for your family, our Bodhi Family Surf Camp is the perfect vacation package for you! We’ll be using this blog to…
A Typical Day: Bodhi Awaken the Inner Surfer
Words by George Frost
What does a typical day here at Bodhi Surf + Yoga look like? Well, that depends on which of our vacation packages you choose. We have a number of different options, each…
How to Overcome Fear and Push Your Limits in the Lineup
Words by Allison Mouret
Every surfer, regardless of their level or abilities, will eventually encounter fear in the sport. This is actually a humbling observation because for everyone, fear can be understood and accepted as a…